Lithium-titanate (LTO) batteries are some of the safest and most robust in the EV and energy storage sectors. However, they have two significant drawbacks: They’re expensive and not energy-dense. This limits their use in applications requiring compact, high-capacity storage. They’re also complex to manufacture, which is the main reason for their high cost.
A Norwegian startup named TioTech is addressing this challenge using a high-performance nanomaterial called TitanB. They created this material by re-engineering titania, a low-cost material used in everyday products like white paint! They can reshape and refine titania at the nanoscale, boosting its energy density and cutting production costs significantly.
We spoke to Anders Teigland, the CEO of TioTech AS, to understand how their technology and processes work. This article contains highlights from our whole conversation.
This interview is part of our exclusive Scouted By GreyB series. Here, we talk to the founder of innovative startups to understand how their solutions address critical industry challenges and help ensure compliance with industry and government regulations. (Know more about startups scouted by GreyB!)
“We’re turning the world’s most boring material into something that could reshape the battery industry.”
– Anders Teigland
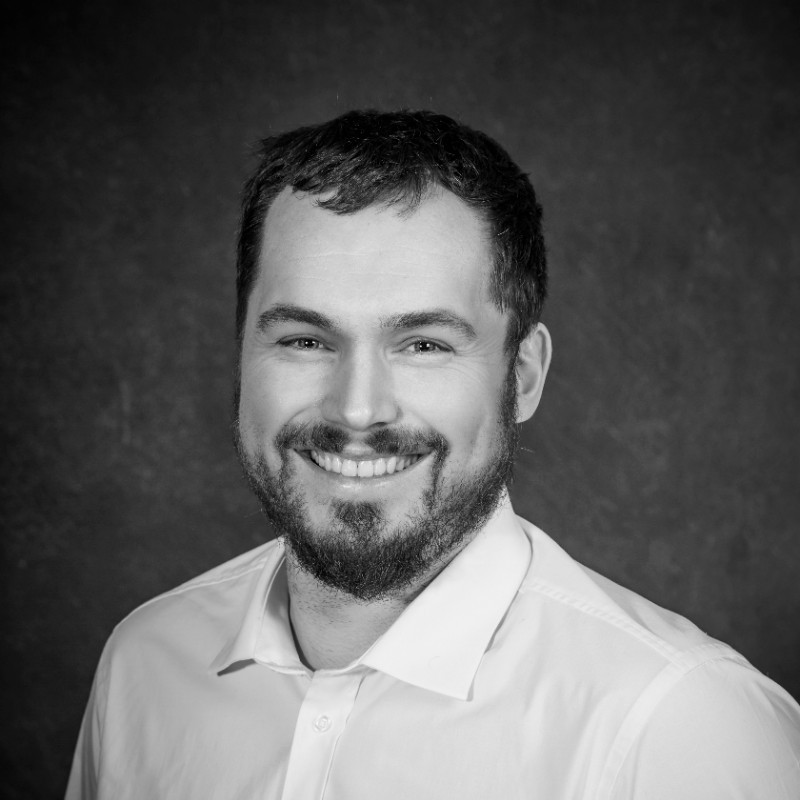
Anders Teigland is the CEO of TioTech AS. Teigland has experience in technology commercialization, operations, and business development, making him well-suited to lead a startup specializing in advanced materials. His previous roles include working at Joma International, where he contributed as an engineer.
How TioTech Is Reinventing Battery Materials With the World’s ‘Most Boring’ Mineral
TioTech has found a way to repurpose a basic industrial material into a high-performance battery component. They achieve this by controlling titania particles’ size, shape, and composition at the nanoscale. The goal? Safer batteries that charge faster, last longer, and don’t break the bank. This new material could be the key to creating safer, more affordable, and longer-lasting batteries, without overhauling existing battery manufacturing systems.
Watch the full conversation here.
Here are the highlights from the interview.
Can you briefly explain what TioTech does and what its role is in the battery materials landscape?
Anders: We’re a materials company focused on nanotechnology. We’re good at controlling particle size, shape, and chemistry, making fine-tuned powders for specific uses. In our case, we took titania—a super common and cheap material—and turned it into something that works incredibly well in batteries. The result is TitanB, a nanomaterial that can help batteries last longer, charge faster, and operate more safely.
What makes titania a viable candidate for battery applications, and how have you modified it?
Anders: The short version is that we’re using titania in an entirely new way. LTO batteries, which are already some of the safest, use similar materials but are too expensive and not energy-dense enough for mainstream use. With TitanB, we aim to increase energy density by 50% while lowering costs. We start with materials already made at industrial scale—like pigment-grade titania (TiO2)—and process them chemically to get the right nano-structure. That means controlling pH, temperature, additives… the whole thing. The result is a battery material that’s better and cheaper to produce.
Who do you consider your ideal customer or collaborator for this technology?
Anders: Honestly, we’re open to working with anyone who sees the value in our actions. But ideally, companies are a bit more integrated—those working in battery development or consortia tackling energy challenges. These partners can help us co-develop and validate the technology faster and get it into the market.
What are the key challenges you’re facing in scaling up production?
Anders: Scaling is definitely where the real work is. We’re moving from batch processing to more continuous, industrial-scale systems. We’ve just bought our first real industrial equipment for our site in Bergen. The biggest challenge is proving that the cost benefits we modeled on paper hold up in the real world. We’re also dealing with hard-to-handle chemicals—strong acids and the like—which makes everything from logistics to safety more complex. It’s not easy, but that’s the reality of materials science.
How easily can TitanB be integrated into existing battery manufacturing processes?
Anders: Yes, and that’s a big part of the value. You don’t need to throw out your whole production line to use TitanB. You might need to tweak some parameters—change a few chemicals or adjust your slurry settings—but overall, the process is compatible. We’ve made the powder to fit into how batteries are made today. We’re still validating everything, especially the electrochemistry, to fine-tune the full battery performance.
How does your process align with current sustainability and recycling standards?
Anders: Sustainability is part of the equation from the start. Our process uses less energy than typical nanomaterial manufacturing methods. The raw material—titania—is sourced from a European supplier with a strong sustainability roadmap. We’re lucky to get it from a French site that uses low-emission energy sources. The tricky part is that Titania is so cheap in bulk that it hasn’t made sense to recycle it before. One risk I see is that batteries get so cheap that recycling economically becomes unappealing again. We’ll need to keep an eye on it as an industry.
What major milestones are you aiming to achieve in the coming year?
Anders: The big focus now is scaling and validation. If all goes to plan, we can start taking the first real commercial steps—building out our production and moving toward becoming a supplier at scale. That means more partnerships, testing, and proof points to show that TitanB is ready for the market.
How do you personally manage the uncertainty and pressure of leading a deep-tech startup?
Anders: If you’re starting a new venture and don’t accept the possibility that it might fail, you will have a hard time. I feel that uncertainty all the time—sometimes daily. It’s tough. You feel the pressure from your team, investors, and the mission. It’s not a sprint, it’s a marathon. What’s helped me is building a solid routine, working with people I trust and enjoy being around, and remembering that most scientific experiments fail. But when something works, it’s magic. You hold onto that.
Meet our Interviewer – Shabaz Khan, Marketing Manager at GreyB
Shabaz Khan, Marketing Manager
Want to find other scalable startups innovating in energy storage? Fill out the form below to reach out to our experts.
Get in touch
Please share your query below