Air travel is fast, but for short distances, it’s inefficient and outdated. Most short-haul flights are costly and burn far more fuel per passenger-mile than modern cars or EVs. The core issue lies in conventional aircraft design: wings bend under pressure, requiring heavy reinforcements that add drag and weight. As a result, planes use more energy just to stay in the air.
A startup named DBT Aero addresses these issues with an efficient aircraft design, known as the Double Box Tail (DBT). Their aircraft promises fuel efficiency of 30 miles per gallon at speeds of 300 mph, comparable to a car but six times faster. It works with all propulsion systems, from electric to hydrogen. Their box-wing design distributes the stress, allowing the wings to stay straighter and lighter, which in turn makes the plane stronger and more fuel-efficient.
To better understand how their technology works, we spoke to Michael Duke, CEO of DBT Aero. This article contains notable highlights from our entire conversation.
This interview is part of our exclusive Scouted By GreyB series. Here, we speak with the founders of innovative startups to understand how their solutions address critical industry challenges and help ensure compliance with industry and government regulations. (Know more about startups scouted by GreyB!)
“If every airplane used our design with the same engines, we’d save 30 billion gallons of jet fuel a year.”
– Michael Duke
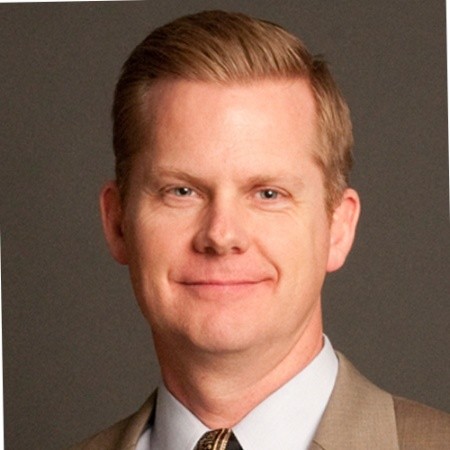
Michael Duke is the Founder, CEO, Director, and CFO of DBT Aero, a startup focused on revolutionizing aviation through ultra-efficient aircraft design. As an aerospace innovator and pilot, Duke has hands-on experience in aircraft design, flight testing, and operations. In 2023, Duke was named “Innovator of the Year” by the Utah Aeronautics Division for his contributions to sustainable aviation.
The Jet of the Future Has No Wing Wobble, No Drag – and Might Save 30Bn Gallons of Fuel!
DBT Aero is a stealth-mode aerospace company pioneering a highly efficient aircraft design. After two decades of development, the startup is preparing to launch a commercial aircraft that flies at 300 mph while delivering fuel efficiency comparable to cars, around 30 miles per gallon. This breakthrough is made possible by their proprietary airframe structure, which significantly reduces drag, eliminates wing bending, and supports future propulsion systems, including electric and hydrogen-powered ones.
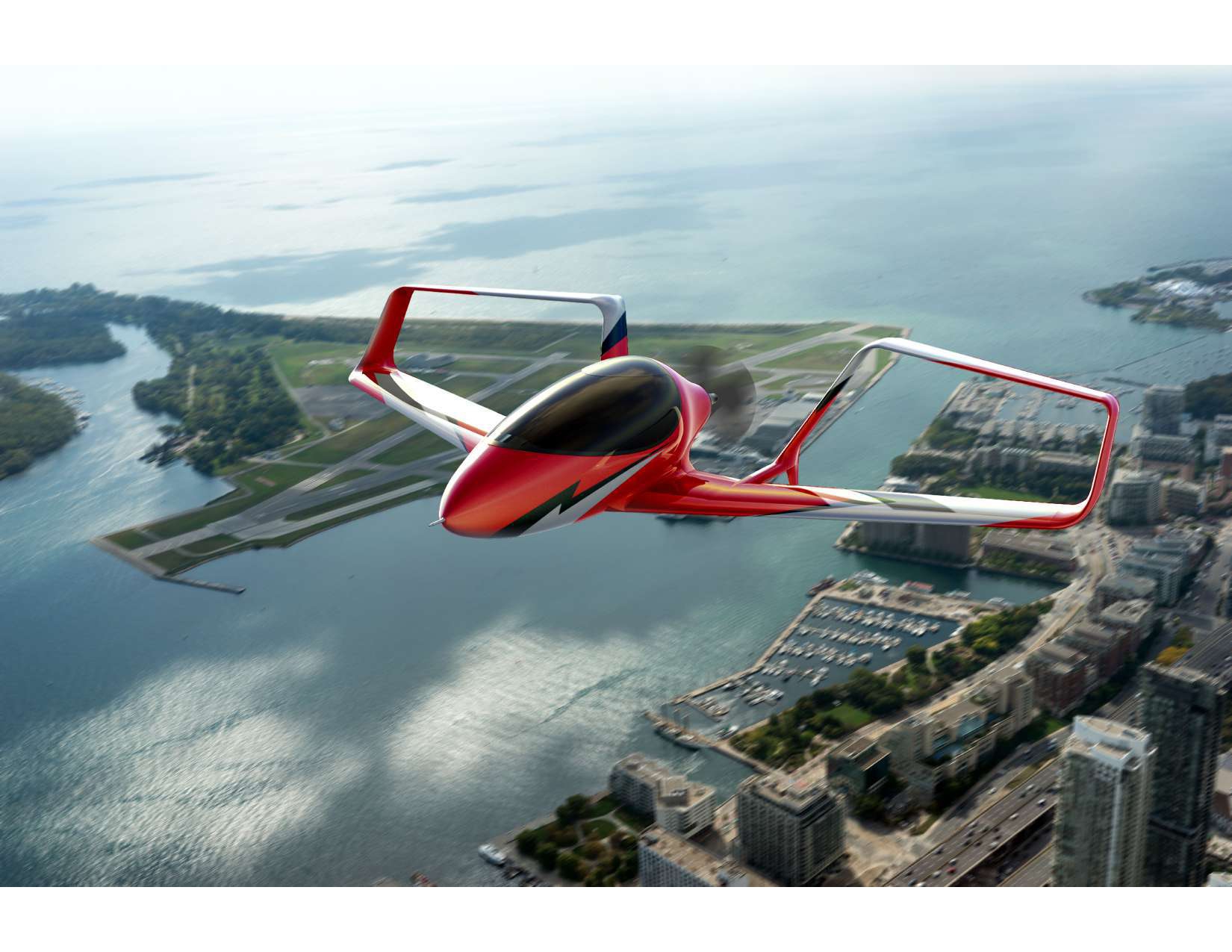
What does DBT Aero do differently from traditional aircraft?
Michael: Our focus is on ultra-efficient flight. We’re optimizing how much movement you get for each unit of energy—essentially, how far and fast you can go per horsepower. Aircraft today either fly very fast or very slow, but the 300 mph range is inefficient and neglected. Our design fills that gap. With our aircraft, you could fly at 300 mph and still get 30 mpg. It’s a game-changer in the mid-speed range.
How are you able to achieve this level of efficiency?
Michael: We combined multiple proven aerospace innovations that had never been integrated before. The key is our Double Box Tail—a unique structure where the tail connects directly to the wings. This eliminates wing bending, resulting in reduced fatigue, improved structural integrity, and consistent aerodynamics. We’re the only ones doing this. People often confuse us with joint-wing designs, but our box tail design performs better and avoids their issues.
What about the long-term durability of your aircraft?
Michael: Our fatigue life is better than traditional aircraft. Traditional wings bend in flight, causing fatigue over time. Our wings don’t bend because the tail structure boxes them in. This rigidity enables you to safely integrate components, such as batteries or hydrogen tanks, directly into the wings without risking stress fractures. Additionally, the absence of bending ensures that aerodynamics remain stable, further enhancing efficiency.
How does your aircraft handle aerodynamics and flight control?
Michael: We designed for natural laminar flow across the entire airframe—wings, fuselage, tails—like what Gulfstream does for wings. We’ve also worked on boundary layer control and non-traditional concepts, such as pressure thrust. The result? Almost zero wingtip vortices, which are a huge drag factor in most planes. Our effective wingspan is 49 feet, but we achieve that with just 32 feet of physical wings, thanks to the box tail.
Why hasn’t this design been widely adopted yet?
Michael: Mostly misunderstanding. People often mistake our design to be the same as a joined winged one and assume we’ll face the same problems. But the aerodynamics and structure are entirely different. We’ve kept quiet intentionally while we’ve proven the design. Now that we’re ready to commercialize, we know we’re offering something no one else has—and they can’t copy it either due to our patents.
What kind of impact does this have on fuel and emissions?
Michael: We’re 30% more efficient at minimum. That applies across propulsion types—battery, hydrogen, turbine, you name it. The design itself boosts efficiency. Our laminar-flow fuselage also gives more cargo or cabin volume without increasing drag. That’s huge for cargo carriers and passengers alike. Additionally, quieter rides, reduced fuel consumption, and lower emissions. Everyone benefits—operators, passengers, and the planet.
Can the design scale to larger aircraft?
Michael: Absolutely. We’ve tested wingspans ranging from 5 feet to 32 feet, including manned aircraft. We even designed a full-size refueling tanker for a submission. The tech scales, but large aircraft would need a partner like Boeing or Airbus to handle aspects such as evacuation compliance. Still, we can serve 9 to 39-passenger markets ourselves, which is ideal for regional travel.
What are the challenges of partnering with big aerospace firms?
Michael: It’s mostly about adapting to new manufacturing methods. We utilize carbon fiber composites to achieve a seamless, turbulence-free surface. That’s different from metallic structures with rivets, which create drag. Additionally, factors such as fuselage volume influence the design of emergency exits. We’re confident these challenges are solvable—just need the right partners.
What is the market opportunity for your aircraft?
Michael: Michael: Massive. In the U.S., for example, ten times more people drive 1,000 miles one-way than fly. Why? Because flying’s expensive and inefficient for short trips. Our aircraft changes that—cheaper, faster, and more sustainable than driving. It makes regional flights not just viable, but preferable. That’s the future we’re building toward.
At this year’s AirVenture, we’re unveiling a commercial aircraft that’s designed to outperform every aircraft currently in production or development. We’re targeting a cruise speed of over 200 knots at 10,000 feet, a 1,000 nautical mile range with a 45-minute fuel reserve, and fuel burn under 9 gallons per hour—translating to more than 25 miles per gallon. The aircraft supports a useful load of over 780 pounds and features a single-lever Full Authority Digital Engine Control (FADEC) system, paired with a constant-speed propeller, for enhanced pilot control.
What sets it further apart are its luxury and safety features: a custom-designed interior with optional livery, premium avionics for Day/Night VFR and optional IFR configurations, and a ballistic recovery chute for added safety. It even includes retractable landing gear for reduced drag and improved aerodynamics.
We’re setting a new benchmark in aviation performance and efficiency, and AirVenture is just the beginning.
Meet our Interviewer – Shabaz Khan, Marketing Manager at GreyB
Shabaz Khan, Marketing Manager
Want to find other scalable startups working on sustainability and efficiency in aerospace engineering? Please fill out the form below to contact our experts.
Get in touch
Please share your query below